March 2024
Modular buildings can offer an aesthetic edge - to match their practicality, sustainability, and cost-efficiency.
The modular building trend has gained significant traction in recent years, its rising popularity due to the fact that they can be pretty cost-effective and, to some, they offer a solution to pressures currently felt in the property sector.
And the good news is modular doesn't need to be boring.
There are examples of modular companies producing architecturally pleasing products suited to the more discerning buyer... like some designers I know.
One example of a company meeting the market just down the road in South Waikato is the recently established Modubuild, whose designs represent a harmonious blend of aesthetic detail and pragmatism.
Their modular spaces are not just visually appealing but are designed with a keen eye on usability and convenience.
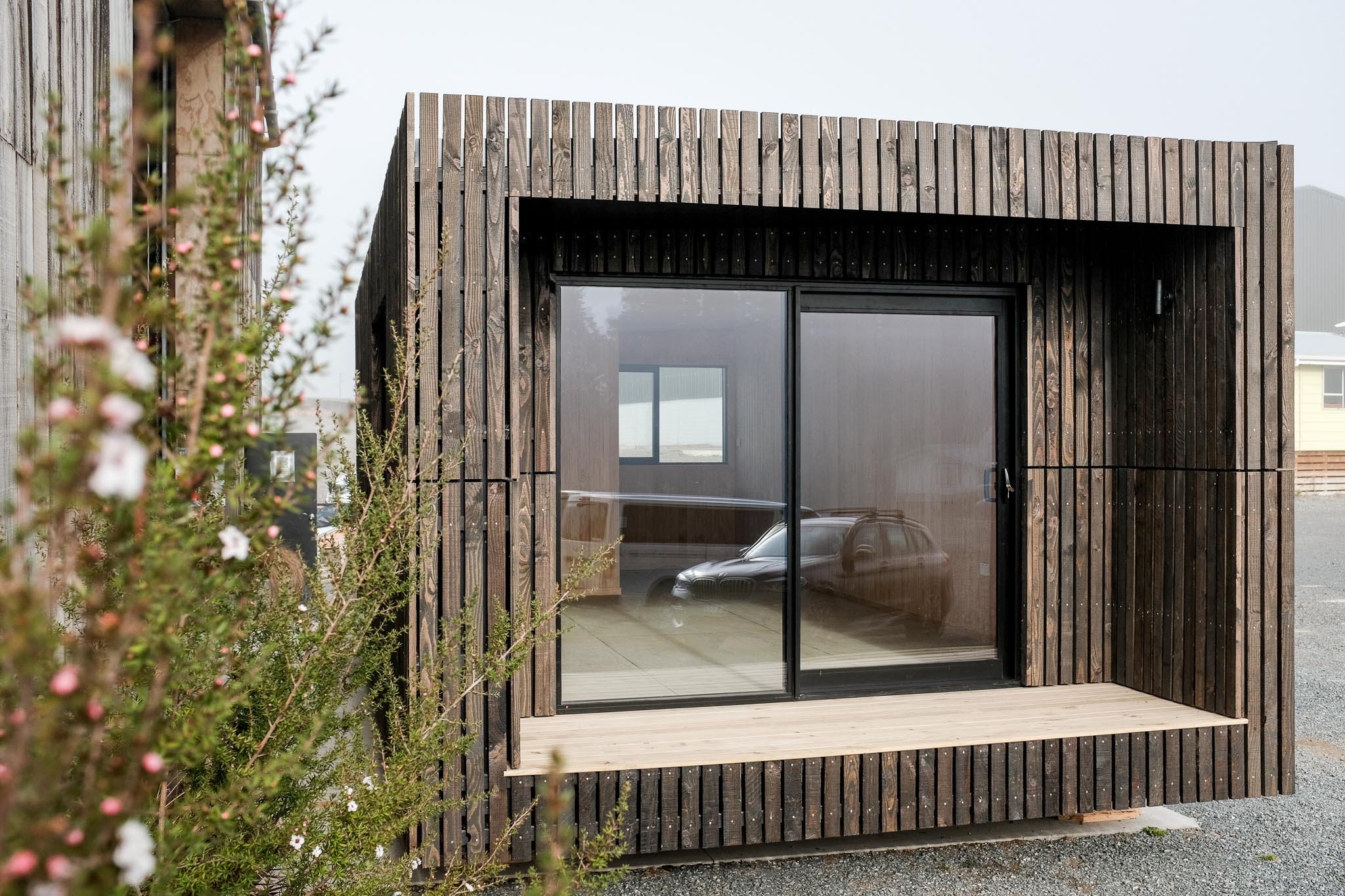
Cost-effective solutions that look good.
You don't need to be a rocket surgeon to understand that off-site fabrication can cost less, and modular construction inherently produces less waste and consumes fewer resources, than conventional on-site building techniques.
Modular also offers would-be homeowners shorter lead times and less construction cost risk, minimising the chances of commonplace site and supply disruptions, which have proven expensive recently.
The strength of these modern, architectural, yet simple structures is their range of applications.
Use cases for modular buildings are only limited by your imagination.
In the case of Modubuild, I understand current applications range from standalone cabins, sleepouts, offices, and baches through to existing building add-ons (that extra bedroom you've needed for some time) and, of course, larger multi-modal residences.
This article shows an example of a standalone module (in this case 30m2) timber-lined studio with bathroom, that is due to be sent on a truck to beautiful Taranaki.
The exterior battens that obscure the blacked-out watertight cladding are sustainably sourced rough-sawn Douglas Fir, stained and stainless screwed.
You could select any number of cladding options, like locally produced timber, or you might fancy an exotic import such as Cedar or Larch, fixed with copper nails - it's your choice.
The factory sits within reach of several redwood mills, so I imagine that's an excellent option.
As many 18m2 modules as you need.
In this case, Modubuild buildings are created by combining 6m x 3m modules - the ideal size for easy trucking – designed and manufactured in the factory, separated for transport, and expertly stitched together on-site.
The buildings come with construction consent and are ready to be placed, most commonly on pile foundations, although customers can opt for a polished concrete floor if they prefer, albeit a slightly more complex scenario.
Services would usually be added once on-site, and consents would be finalised by the customer with their local council as required. There is a degree of customisation available for customers who have their own sparky, plumber, etc., and prices obviously reflect the customer's requirements.
Because modular systems can deliver both form and function, they are increasingly popular with architects, developers, and homeowners - and will continue to rise in popularity.
Perhaps modular will become a partial remedy to our nation's accommodation shortage and the cost of housing in this country.
Time will tell.
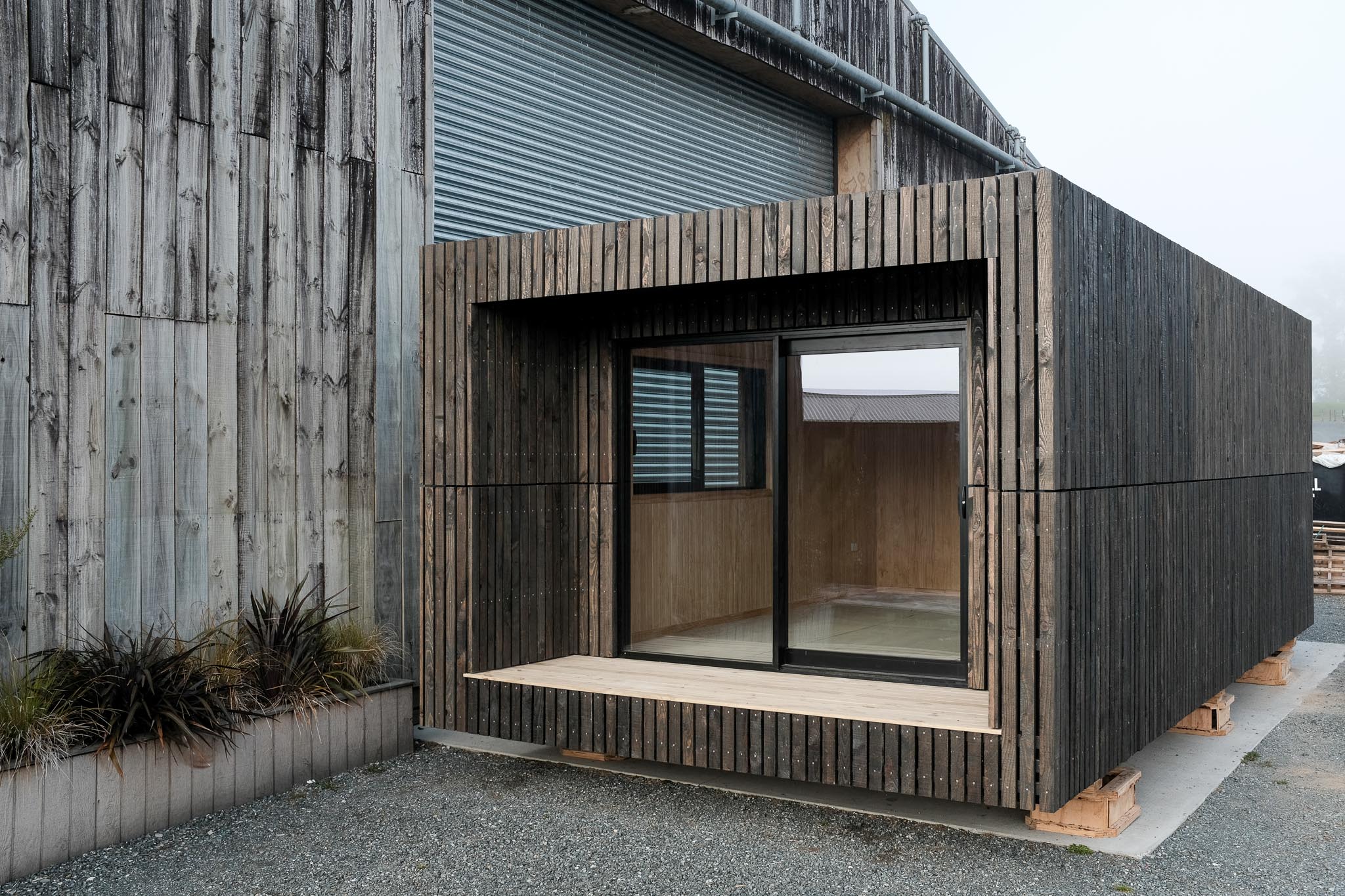
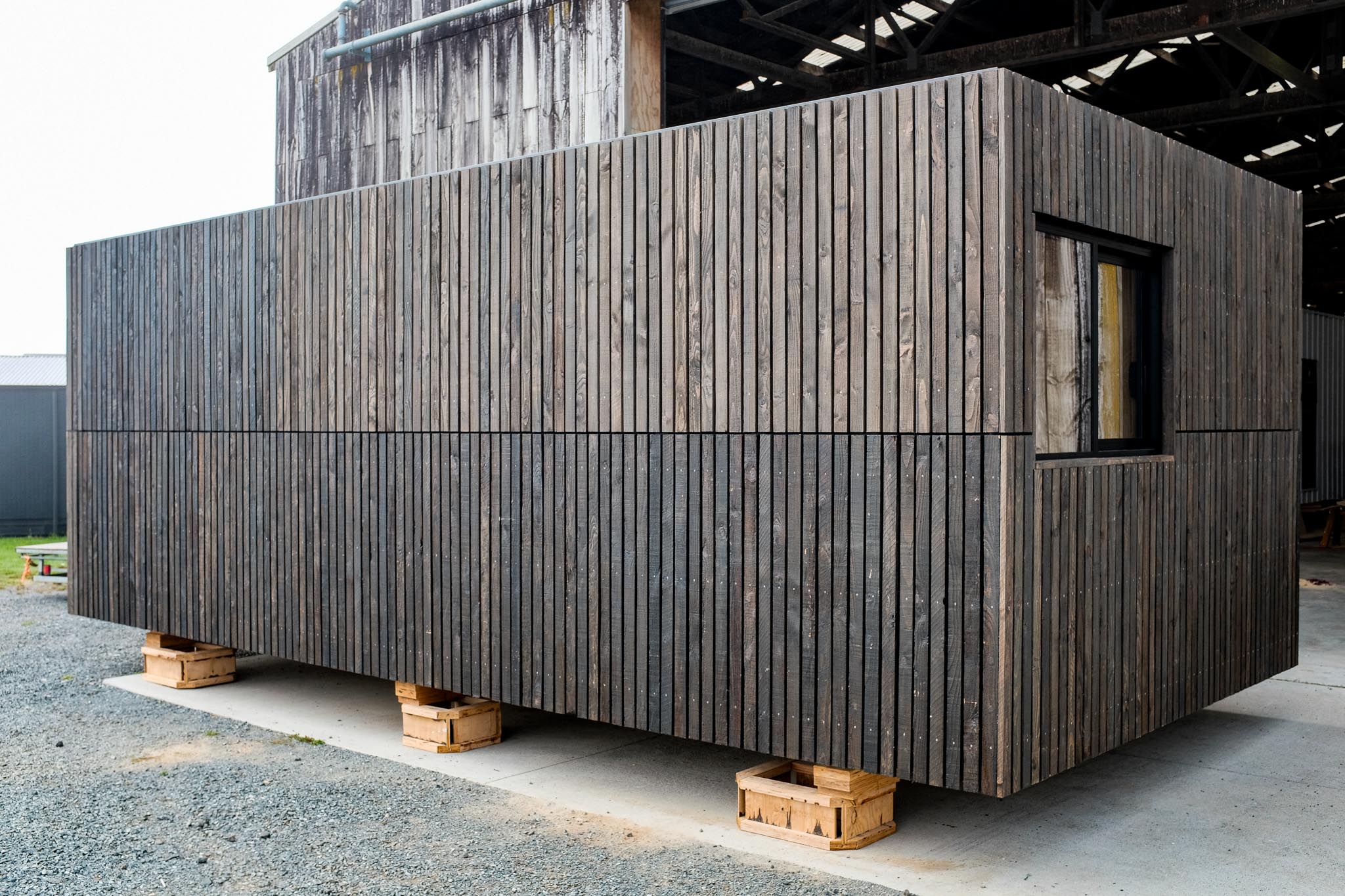
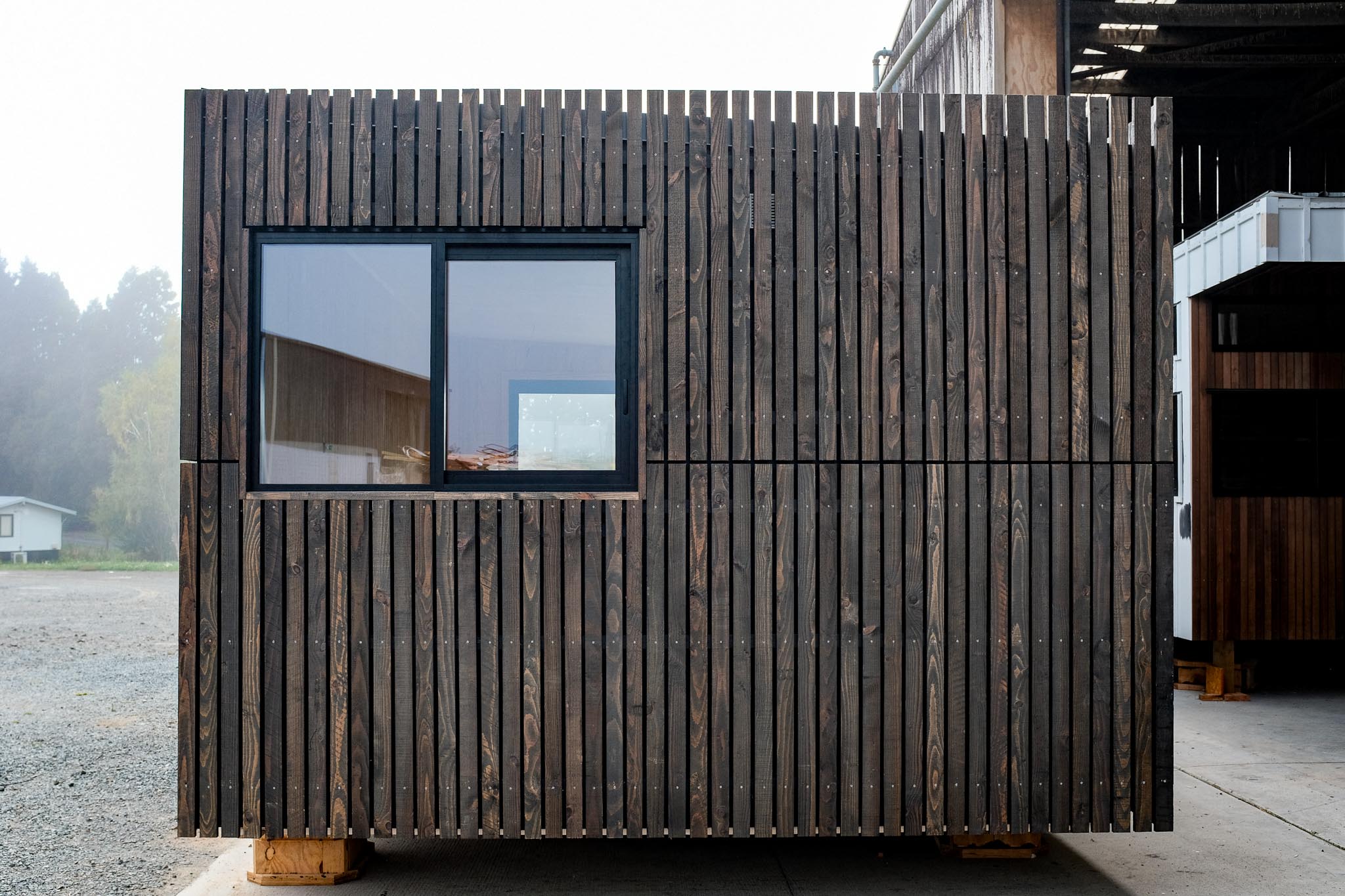
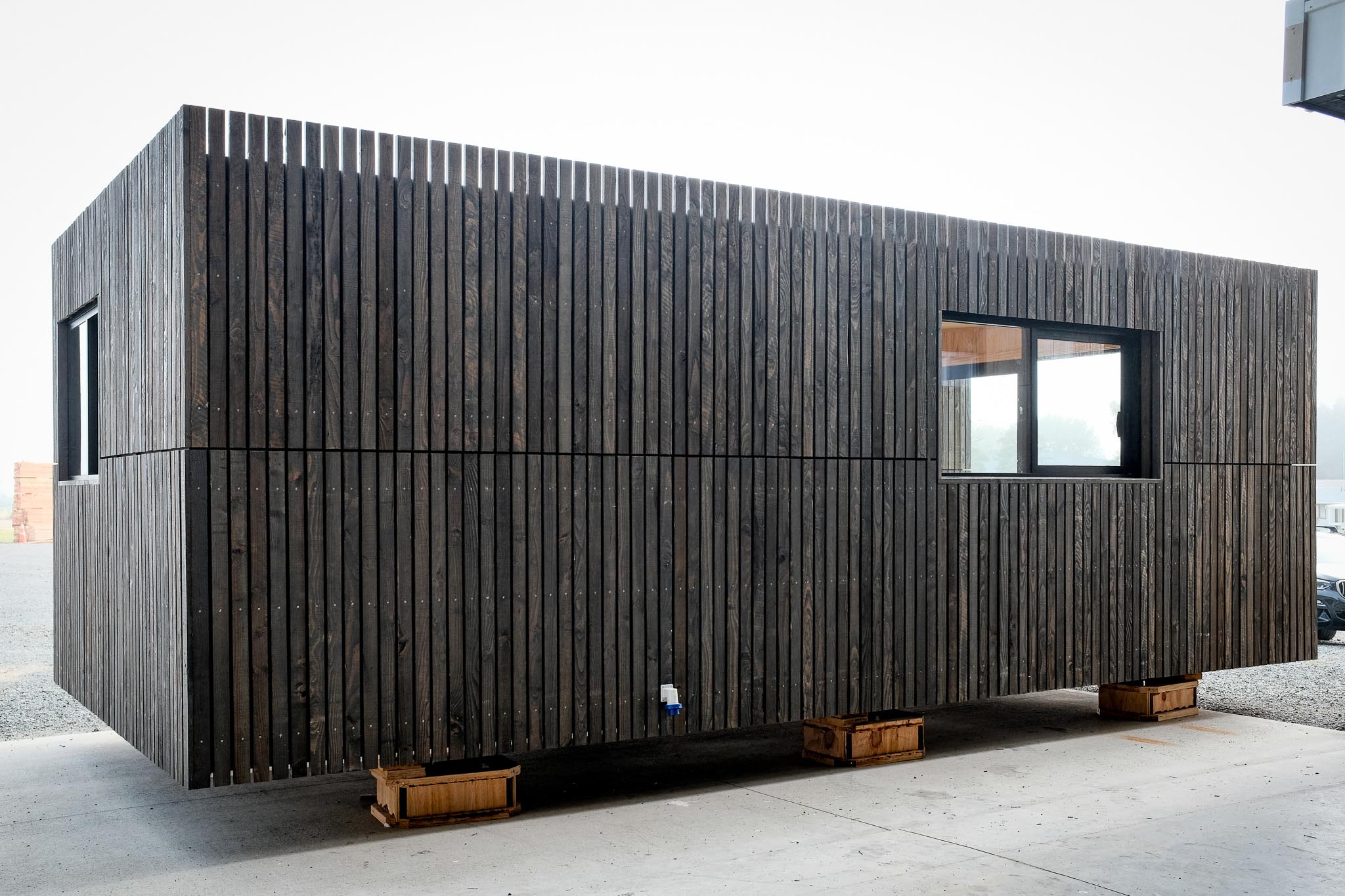
All images (c) MrWolfe
As an aside, I really like the fact that Modubuild's factory sits within a historic timber building of some considerable size, as the images show.